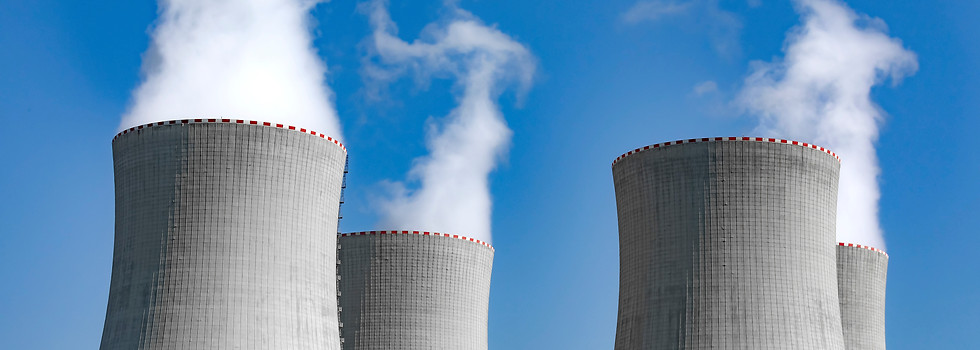
Cooling Towers
Cooling tower monitoring example
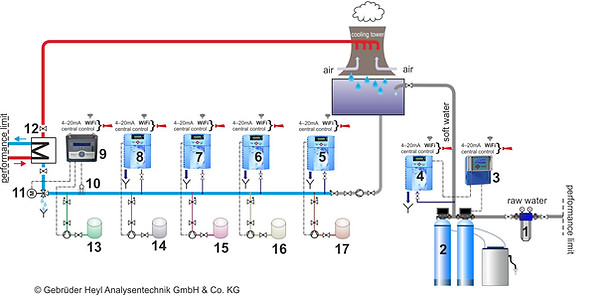
1 Pre-filter
2 Softening system
3 Control Softmaster MMP1
4 Hardness monitoring Testomat® 2000/ECO
5 Chlorine monitoring Testomat® 2000 CLT/F
6 Bromine monitoring Testomat® 2000 Br
7 Phosphate monitoring Testomat® 2000 PO4
8 Polymer monitoring Testomat® 2000 Polymer
9 Control of biocide dosing MultiControl CT
10 Conductivity probe
11 Motor valve
12 Plate heat exchanger
13 Biocide
14 Polymer
15 Phosphate
16 Bromine
17 Chlorine
Control and Monitoring Solutions for Recooling Plants
Effective cooling water control and monitoring stand as essential elements for the advanced energy and hygiene-compliant operation of cooling towers.
Plant Operator Responsibilities
Industrial cooling systems play a critical role in rapidly dissipating excess heat from production processes and buildings. Despite recent economic and hygienic enhancements, concerns persist regarding malfunctions due to deposits and corrosion, leading to issues such as the rapid spread of legionella.
For operators of evaporative cooling systems, prompt action is crucial to prevent mineral-based, corrosive, and biological accumulations, including legionella and pseudomonads. Plant operators must be well-versed in these responsibilities, as neglecting them may result in legal consequences. Ensuring trouble-free, economical, and hygienic cooling tower operation necessitates continuous water monitoring and system conditioning.
Key Monitoring Focus Areas
In cooling systems, whether open, semi-open, or closed loop, evaporation is inevitable, leading to elevated levels of salt concentrations in circulating water. Salt and mineral levels can trigger limescale accumulation, corrosion, and deposits within cooling towers and circulating water systems. This particularly impacts components such as drip collectors, trickling filters, distribution channels, and heat exchangers. Biological challenges, including algae and biofilm formation from supply water and ambient air, further exacerbate the issue.
Notably, biofilms and mineral deposits, such as calcium or silicate, have comparable energy impacts. A 1 mm biofilm layer or mineral deposit can result in a 30% loss in efficiency, translating to up to a 12% increase in energy costs.
In conclusion, a monitored online cooling tower system ensures hygienic, efficient operation, reducing the risk of malfunctions.